Overview
While we are moved by the girl Liz Murry story in the film Homeless to Harvard, the film demonstrates between the lines what Harvard University means for those who pursue academic achievement. This week, we will introduce stainless steel application in the new Science and Engineering Complex (SEC), a new center constructed by Harvard for its John A. Paulson School of Engineering and Applied Sciences (SEAS).
The Science and Engineering Complex
The Science and Engineering Complex (SEC), located on Harvard University’s Allston campus, was completed in the fall of 2020 and opened to full capacity until the Fall 2021 semester. The pandemic slowed down the process but offered extra time for an orderly transition.
SEC is an 8-story, 544,000-square-foot building that integrates classrooms, active learning labs, faculty labs, a makerspace, as well as a café, and plenty of room to foster a sense of community and to promote interdisciplinary research, learning, and innovation.
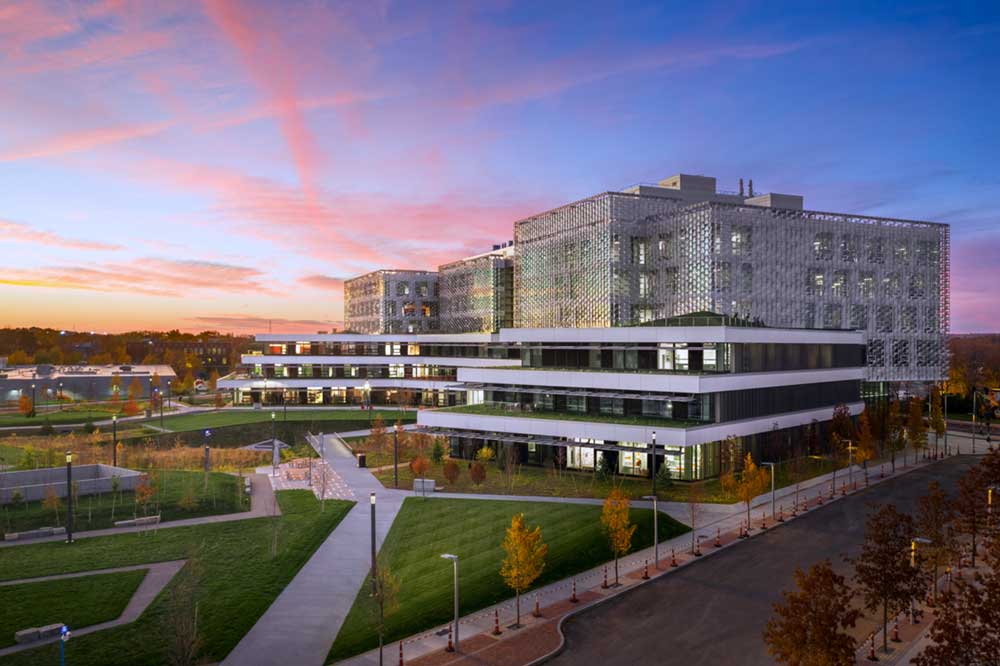
The 500-year Building
SEC is "a 500-year building" (Jonathan Shaw, 2021), which sounds a bit unimaginable. This remark doesn’t suggest a verified service life. Instead, it delivers three messages: 1) the structure’s anticipated longevity; 2) a climate-resiliency perspective where a 500-year flood is considered for the design; 3) years passed (the design work started in 2007) with the republished 500-year flood maps for the district from the first design till the final one.
The Design and the Latest Technology
SEC is designed by the architecture firm Behnisch Architekten. Committed to the “healthiest building on the Harvard campus,” the design has earned both LEED Platinum and Living Building Challenge (LBC) Petal certification in Materials, Beauty, and Equity.
The optimal use of natural resources prompts the innovative and sustainable solutions. The building is renowned for its exterior envelop, designed to shelter solar heat in warm seasons and admit beneficial sun during cold days. This solution gives rise to the world’s first hydroformed tensile façade system. The adoption of water-based heating and cooling system allows the building to consume only 1/3 the energy of comparable air-driven systems.
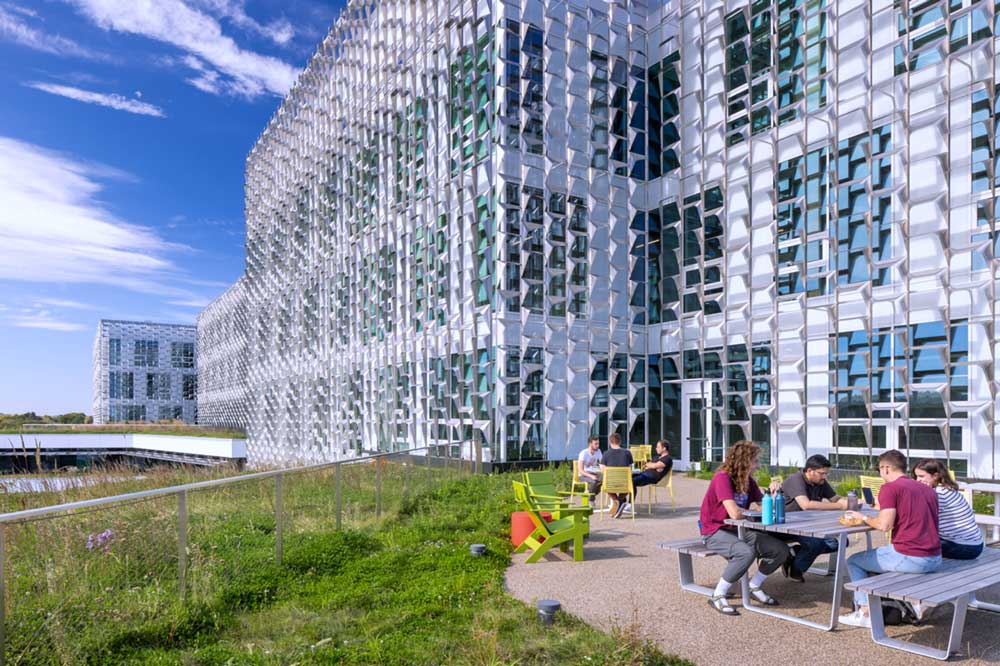
In terms of day lighting, the building’s size posed extra challenges. For a building wide and deep like SEC, natural light could penetrate only about 1.5 times the floor-to-floor height. It would undoubtedly increase the energy load of illumination. That’s how the design team came up with a pair of 8-level glazed atria for both the maximum use of natural light and connecting three four-story volumes harmoniously and continuously.
With the energy-conscious HVAC and lighting systems and five acres of vegetated roof terraces, the façade delivers as a landmark that combines both performance and aesthetics.
Stainless Steel Applied in SEC
There are 12,000 precisely milled stainless steel panels in 14 different shapes, with each panel sized at 750mm*750mm and weighted less than 4.5KG. These panels are shaped and processed from 1.5mm stainless steel sheet by hydroforming and laser cutting. Hydroforming is commonly used for industrial parts and automatic industries, but the application in fabricating these panels is the first of its kind.
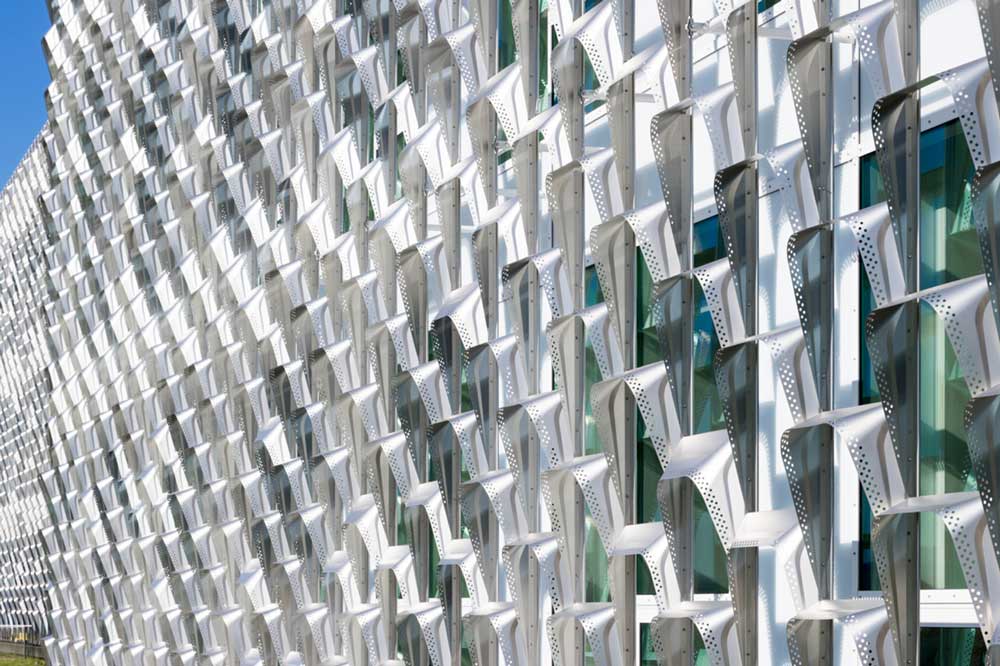
Why Stainless Steel Material?
Stainless steel is chosen over aluminum because applying stainless steel material can significantly reduce carbon dioxide emissions, as table below listed.
Material | Carbon Dioxide Emissions |
---|---|
3mm aluminum panels | 1790 tons |
2mm stainless steel panels | 234 tons |
1mm stainless steel panels | 117 tons |
Back to stainless steel material itself, it embodies several advantages that other metals can hardly compare. Firstly, stainless steel is readily formable into the desired shape with minimum amount of material, thus it saves cost. Secondly, applying stainless steel material can reduce embodied carbon. Thirdly, stainless steel material is harmless and recyclable. It is eco-friendly with long service life.
Why 1.5mm Thickness Stainless Steel?
1.5mm proves to be the ideal thickness among the three-tested thicknesses 1mm, 1.5mm and 2mm. Although 2mm-thickness stainless steel panel has the highest strength that supports the structure, it is difficult to get the exact shape, especially at the folds and corners. 1mm-thickness stainless steel is easily shaped, but it can hardly provide stable support. The application of 1.5mm thickness stainless steel panel can achieve the best performance.
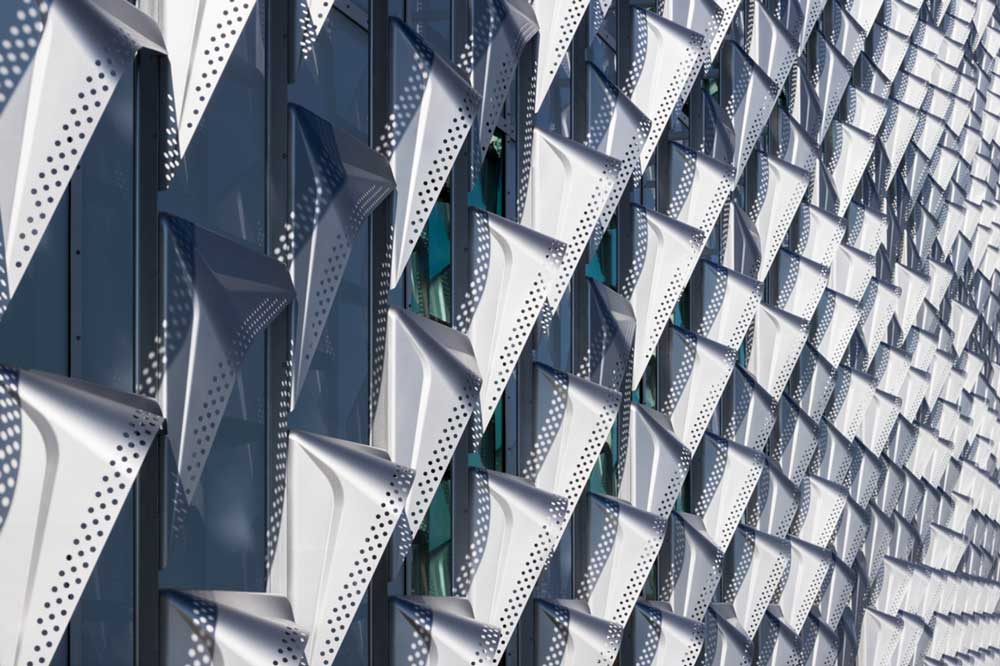
Why 316L Stainless Steel?
316L stainless steel is chosen for it can withstand extreme climate changes. 316L stainless steel is superior to 304 as it contains extra 2% molybdenum which the 304 doesn’t. It can resist the rust generated from the deicing salt used in Boston during the winter.
For SEC building to apply the hydroforming processed panels, 316L stainless steel is advantageous as it features good ductility which allows it to withstand large deformation without breaking. Besides, 316L stainless steel exhibits the required strength which makes it ideal for applications where high structural integrity is required.
Stainless Steel at CIVMATS
In the case of SEC, stainless steel panels possess superior strength and light weight, necessitating the minimal tensile support structures. Each panel is bolted directly to a vertical 316L stainless steel tie rod. This light and concise structure allows for the maximum use of natural light. While it provides the best unobstructed view for the people inside the building, this structure can reduce illumination cost simultaneously.
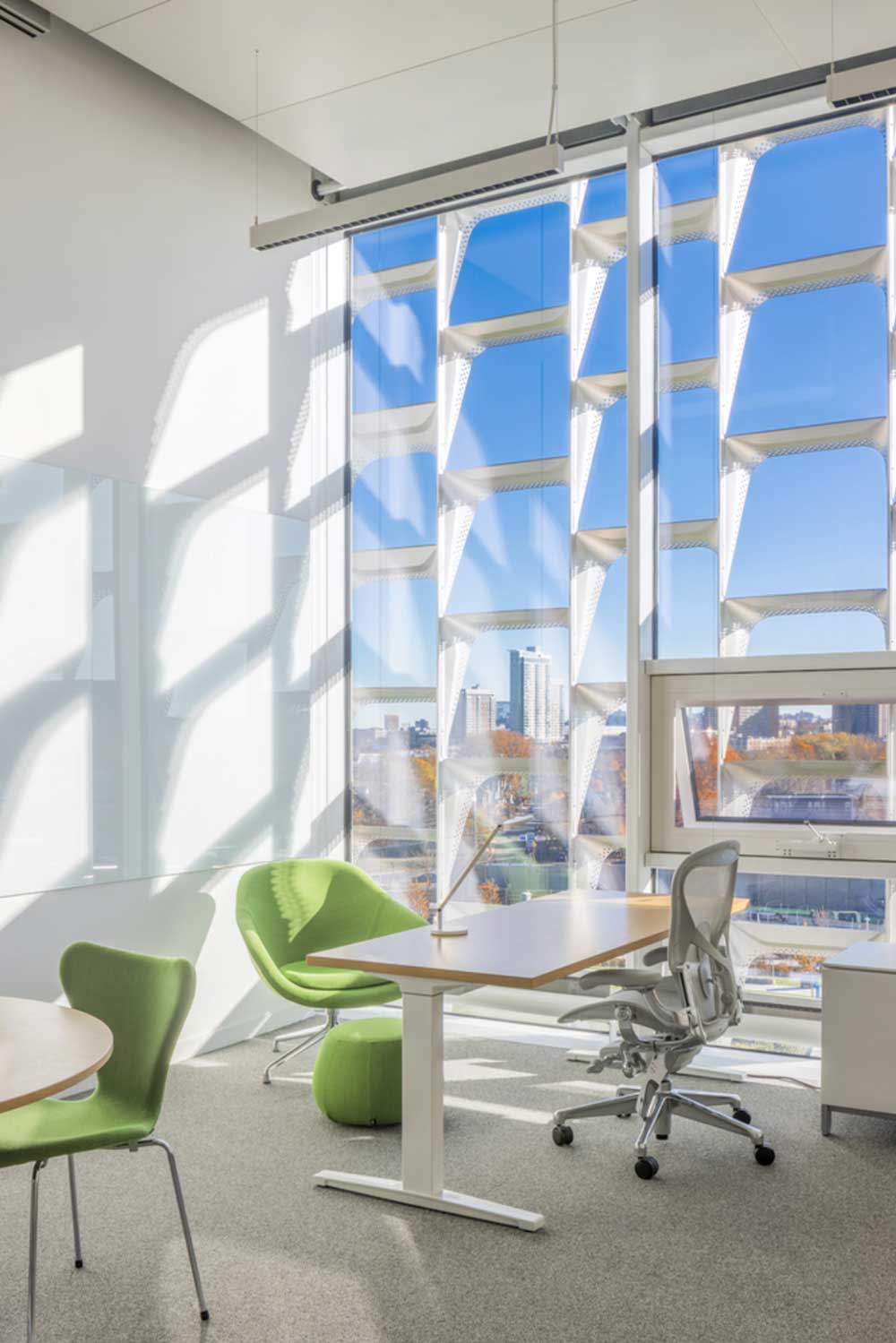
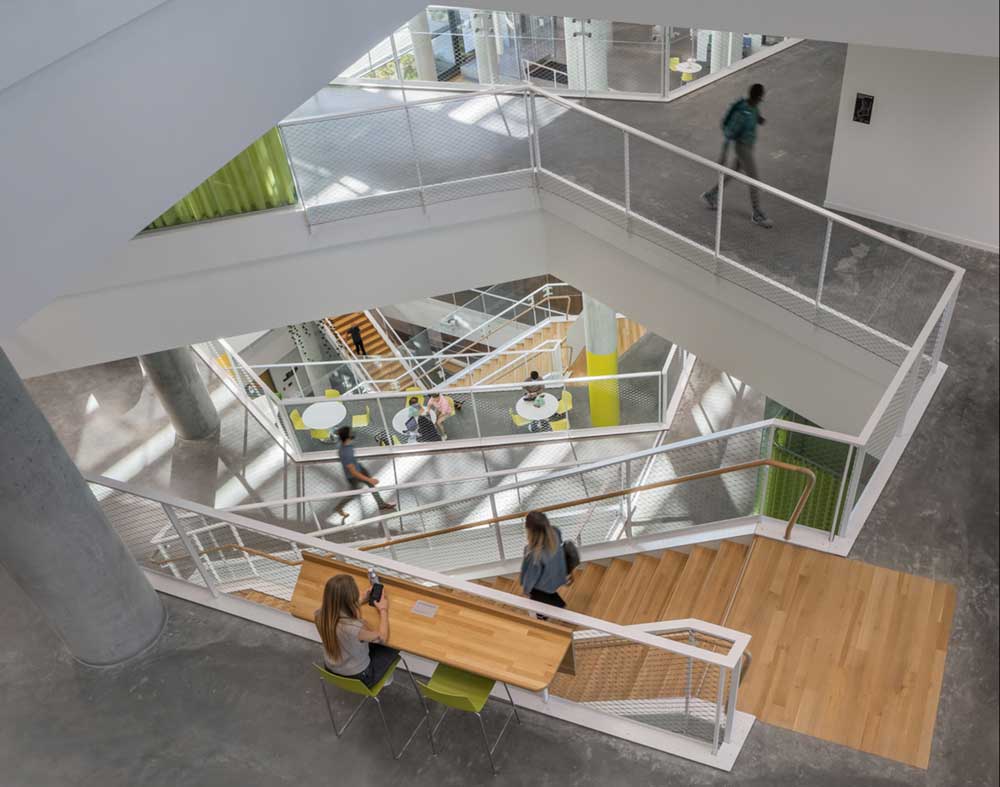
At CIVMATS, we stock famous brands stainless steel coils and sheets which are ready for processing per your requirement. We also manufacture stainless steel long products for your specific project demands. Welcome for your free consultation, enquiry and purchasing.