Introduction
Nickel alloy is a heavy non-ferrous metal material, based on nickel and composed of other alloying elements. In order to further improve the physical and chemical properties of nickel, and to meet the requirements of scientific technology and industrial development, it is necessary to add an appropriate amount of alloying elements into nickel. According to applications, nickel alloy mainly includes: 1)nickel alloy for electric vacuum, 2) nickel alloy for thermocouple, 3) monel alloy, 4) nickel-niobium alloy, and 5) nickel-based catalyst alloy for synthetic diamond. Nickel alloy ingots or castings are mainly fabricated through vacuum casting. The ingot is first subjected to hot rolling, extrusion or forging, then to intermediate heat treatment. After that, it will be subjected to rolling or stretching, and at last processing into a desired finished product. Another two methods are also used for some nickel-based super alloys to make parts: 1) casting directly; 2) powder metallurgy.
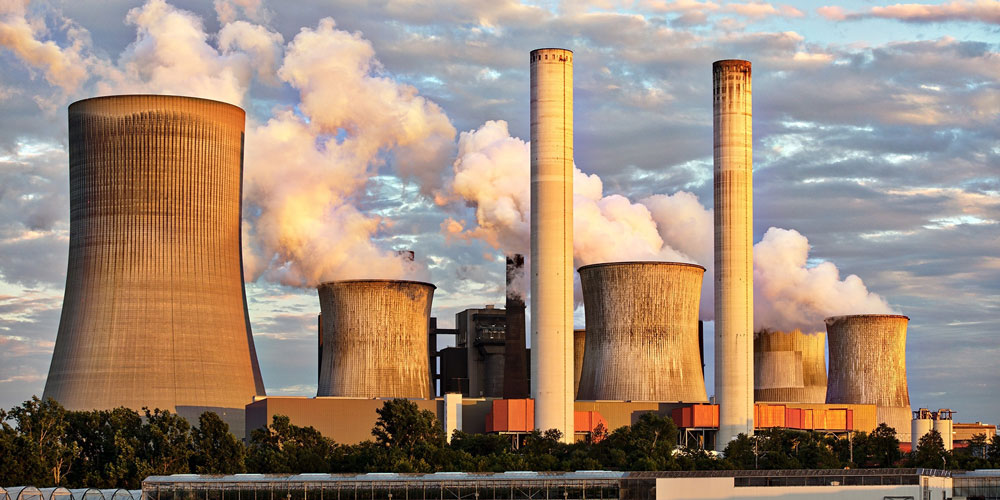
Alloying elements, Categories, and their roles
The alloying elements added are mainly categorized into two groups: 1) those solution-strengthening elements capable of forming solid solutions with nickel, such as copper, cobalt, iron, chromium, molybdenum, tungsten, manganese, etc.; 2) those phase-strengthening elements capable of forming intermediate compound with nickel, such as aluminum, silicon, germanium, titanium, zirconium, hafnium, vanadium, niobium and tantalum. Apart from these elements, some trace elements are sometimes added for specific purposes and uses; these trace elements include rare earth elements, boron, magnesium, calcium, barium, and strontium.
The roles each category play can vary from one another. For example, adding solution-strengthening elements will lead to 1) enhanced strength, hardness, shock resistance, corrosion resistance, oxidation resistance, high temperature strength and also certain physical properties such as magnetic properties, thermoelectric potential and electrical resistivity; 2) reduced expansion coefficient, thermoelectric potential and temperature coefficient of resistance (TCR) against copper.
If phase-strengthening elements are added into nickel, the material properties, especially high temperature mechanical properties, corrosion resistance and certain physical properties will be further improved. The addition of trace elements in the alloy is expected to eliminate the adverse effects of harmful impurities that might have on the alloy properties, or to obtain some special physical properties for the alloy, or to strengthen the alloy grain boundaries, for sake of better alloy performance and prolonged service life.
Applications:
- 1. Heat treatment industry, such as furnace rolls, bell furnaces, annealing furnaces and etc.;
- 2. Calciner used for calcination and production of high-performance corundum, calcination of chromite ore, production of ferrochrome alloy, and recycling nickel used as a catalyst in petrochemical industry;
- 3. Chemical and petrochemical: used to prepare a new steam cracking crude gasoline furnace to produce hydrogen;
- 4. Automation device, such as catalytic support systems, spark plugs;
- 5. Cleaning equipment for the nuclear industry, such as nuclear waste removal;
- 6. Iron industry, such as the direct reduction of iron ore technology and the production of titanium sponge.
Contact
CIVMATS produces Nickel alloy products, such as pipes & fittings, bars. If you are in demand, please contact us:
- Company: CIVMATS CO., LIMITED
- Phone: 86-519-81809659
- Fax: 86-519-81809959
- Email: [email protected]
- Address: 10th Floor, Xin Cheng Nan Du, Wujin District, Jiangsu, China
- Website: www.civmats.com